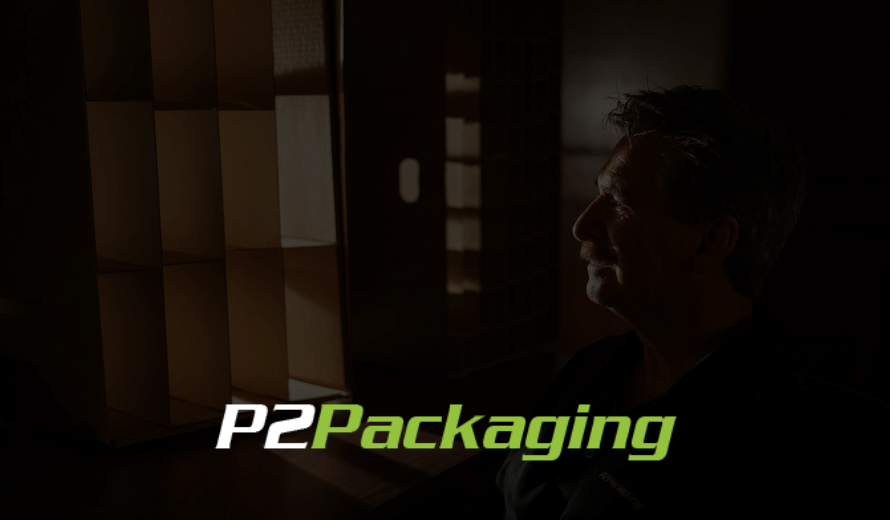
October 08, 2021
How a simple box design is saving the auto industry millions of dollars: ‘It’s amazing’
How a simple box design is saving the auto industry millions of dollars: 'It's amazing'
P2Packaging owner Rudy Youell sits last month with a couple of versions of his P2 product box. They are custom built to fit dimensions of products and fold flat after use. Ryan Garza, Detroit Free Press
Phoebe Wall Howard | Detroit Free Press | Published Oct. 6, 2021
This is a story about a box.
That’s it, just a box.
“It’s not rocket science,” said Rudy Youell. “It’s almost so stupid it’s ridiculous. But it’s saving so much money it’s amazing.”
His simple box design is saving the auto industry tens of millions of dollars behind the scenes in production, shipping and labor costs just as companies are navigating a land mine of supply chain disruption and unpredictability that inhibits earning power.
So, imagine if every box Amazon shipped could be reused. Not crushed and recycled after one shipment but actually used again and again to ship items as many as six times and maybe even 10. No plastic. All cardboard. Sustainable.
Consider the dollar savings, not to mention trees that go uncut for cardboard.

P2Packaging owner Rudy Youell outside of Anchor Bay Packaging in New Baltimore on September 21, 2021. Ryan Garza, Detroit Free Press
Youell, 64, of Columbus, Ohio, has worked in the corrugated box business for nearly half a century. He and his father owned American Corrugated, which served automakers and auto suppliers from six locations in five states between 1980 and 2015.
These days, Youell owns the patents for a simple yet unique box design called P2 Packaging that’s licensed to companies in Michigan, South Carolina and Indianapolis and used to ship car parts all over the U.S. and the world.
The boxes are shipping automotive interior trim components between Mexico and the U.S. for pretty much every auto manufacturer — Ford, General Motors, Stellantis, Tesla, Volkswagen, BMW, Mercedes, Kia, Volvo, Dodge Ram, Nissan.
Imagine parts for something like your vehicle dashboard. Now you get it.
No, this box isn’t brand new. Youell said he patented the design and in 2016 began selling it. Now, five years later, it’s a success that marries efficiency with cost savings with an eye toward sustainable materials use.
The patent specifically covers the design of the box partition and the way it’s manufactured, assembled and glued. For example, box dividers inside the package collapse and stay with the box — unlike traditional boxes and partitions, which are not attached.
Most people are aware of boxes that have detached pieces like what’s used to distribute and transport liquor and wine. This P2 design keeps parts together.

Andrew Hurley, seen here on Sept. 22, 2021, is an associate professor at Clemson University and founder of packaging school.com. “Think about the automotive space. Some vehicles have 30,000 parts and some parts have seven packages. A car company has to manage more packages than they do car parts.” Provided by Andrew Hurley
F-150 and Wrangler and Cadillac
This box is carrying parts for everything from the Ford F-150 and Expedition to Jeep Gladiator and Wrangler to GMC Acadia and Cadillac.
Imagine, for example, the bestselling Ford F-Series pickup. Each truck has at least two doors, many of them four doors, and Ford built 1,073,776 F-Series in 2019.
Do the math. That’s a lot of parts.
It illustrates the magnitude of packaging and shipping.
“It’s crazy,” said Andrew Hurley, associate professor at Clemson University and founder of packagingschool.com. “Think about the automotive space. Some vehicles have 30,000 parts and some parts have seven packages. A car company has to manage more packages than they do car parts.”
But the simple box changes everything.
While Michigan State University is recognized for its packaging programs, Clemson has developed a subspecialty in automotive design packaging that has been especially helpful to development of his product, Youell said.
“The package is very simple. And the beauty of it is that it’s a returnable package using expendable materials,” Hurley said. “You look at Amazon boxes, which have one purpose in life: To go from Amazon to you. But this P2 Packaging, well, I got to take a tour of a parts manufacturer and saw it being used. There’s no bubble wrap or wadded-up paper. You don’t have to track it or worry about people stealing it. If you lose it, no big deal. Just way past what you’d expect of a brown box.”
Thing is, the corrugated fiberboard container has been around since the 1800s.
These days, automotive companies are looking anywhere and everywhere for ways to save money and pass those savings along amid pain caused by COVID-19 factory shutdowns and semiconductor chip shortages.
Margins matter more than ever.

Various P2 product boxes designed to fit parts made by P2Packaging sit on display where they are assembled at Anchor Bay Packaging in New Baltimore on Sept. 21, 2021. Ryan Garza, Detroit Free Press
How it works
This disposable box has customized walls for quick collapse. On average, each box design may be reused six times, according to the company and two customers interviewed by the Free Press.
By custom designing parts to carry hundreds and thousands of car parts, there is no empty space that requires filler. Or, in the words of packaging experts, no one is paying to transport air inside the boxes. Every inch is packed.
Fewer boxes transport more materials. Fewer people are needed to haul fewer packages. Less factory space is needed to store boxes. Recycling costs plummet. The impact on the environment, too, is notable.
Something as basic as a glued insert gives a cardboard box 68% more space, so more parts can get packed in. The box folds up and can be used as many as10 times, with color-coded markings on the side to track number of uses. Old corrugated paper shipping boxes used by auto suppliers are bundled and recycled after a single use.
The box design also is stronger, so it doesn’t crush. One automotive client said the box eliminated 58 truckload shipments annually.
Ford, Tesla, Kia benefit
Automakers and their suppliers spend huge money on moving parts between factories.
For example, a parts maker ships a part from its factory in Mexico to an assembly plant in Michigan using a cardboard box. It’s usually just emptied, crushed and recycled. But now with a glued insert, it can be folded up flat and shipped back on pallets to the factory in Mexico to be used again.

Photos show the difference in the flattened, still assembled P2 product boxes over traditional boxes after use. Ryan Garza, Detroit Free Press
“As a packaging engineer, not a whole lot that comes down the pike moves the needle,” said David Colclough, a Michigan State Packaging Engineering graduate who has spent 30 years in the automotive packaging industry. He is the North American packaging buyer for Yanfeng Automotive Interiors based in Holland, Michigan.
“All the stuff is just mundane purchasing and packaging,” he said. “But this P2 product, I can’t emphasize how beneficial it’s been to Yanfeng. When you come across something that literally saves millions of dollars, it’s just not something that you encounter very often. It surprises me that not everybody is using this product. It’s so simple.”
The box is used to ship products between Mexico and the U.S. mostly, including Michigan, Ohio, Kentucky and Tennessee, Colclough said. “It’s used for a lot of Ford product, a lot of Tesla product, Kia, and BMW.”

David Colclough, seen here in 2020, is North American packaging buyer for Yanking Automotive Interiors based in Holland, Michigan. He said the simple P2 Packaging box is an industry game changer because it helps save so much money. Provided by David Colclough
Over the past 26 months, Yanfeng has seen a payoff with the returnable boxes.
“Part of the beauty of P2 is the fact that it’s so simple,” Colclough said. “Rudy has joked that he can’t believe someone didn’t come up with this 50 years ago. It’s nothing radical. We tested to make sure there was no parts damage. This is saving us literally millions of dollars.”
Measuring savings on efficiency is hard, he said.
“But you get twice as many parts in a box and you’re moving half as many boxes,” Colclough said. “The potential cost to the automobile industry could be hundreds of millions or even a billion dollars.”
‘Staggering’
This box has made a big difference.

Larry Ross, program logistics manager for North America operations at Faurecia Interior Systems, said a simple box design is transformative for cost savings in the auto industry. Provided by Larry Ross
“The numbers are staggering,” said Larry Ross, program logistics manager for North America operations at Faurecia Interior Systems, who is based in Auburn Hills.
Everything is intended for long-distance transport of parts. The companies are shipping wrapped components in vinyl or leather, such as armrests or bolsters that go on doors or instrument panels. So-called “trim pieces” in industry jargon.
These boxes are not used to ship huge pieces but, rather, a zillion little bits.
“Now we’re comparing the one-way box to P2 and it’s green. We reuse and no longer throw material into the dumpster daily, compared to what we did before,” Ross said. “When you can get twice the amount of parts on a truck, the numbers are staggering. We’re gaining efficiencies from just a box.”
Selling this simple idea hasn’t always been easy.
“There were nonbelievers,” Ross said. “They were just like, ‘This isn’t going to work. A box only makes it one way.’ I’m like, ‘Let’s just try it.’ I went to three cities in one day following around the loads. To get everyone convinced is challenging. But the boxes still look brand new after shipping three times. We’re seeing six to eight uses, no problem. We have a little checkbox on each box where you mark an “x” on 1 to 10.”
Every little detail matters when it comes to carefully cutting costs, he said. The boxes even come with special cutters that prevent damage while opening.
Estimates for clients can reach hundreds of thousands of dollars in packaging as well as transport costs for a single vehicle, manufacturers told the Free Press. The companies that revealed client detail asked that they not be identified for competitive reasons.

Anchor Bay Packaging in New Baltimore assembles P2 product boxes made by P2Packaging that can be used up to 10 times. Ryan Garza, Detroit Free Press
Making a miracle
Anchor Bay Packaging in New Baltimore is one of the companies licensed to manufacture the corrugated box for custom orders. Colin Tripp, account manager, said his team custom designs and manufactures the boxes for shipping.
Anchor Bay Packaging in New Baltimore assembles P2 product boxes made by P2Packaging that can be used up to 10 times.
“Typically, a customer will give us a part, a picture of a part in your car, like an armrest, and we design the P2 Packaging to fit that part,” Tripp said. “When you have to buy plastic containers, that’s costly. And everybody in the auto industry wants to go green.”
He added, “This is a game changer. It services a niche. Anytime you can knock something down, return it flat and get multiple uses out of it — this is the item that does such a thing.”
The man behind the box
For his whole life, it seems, Youell has been part of the auto industry.
“My dad has always been in the packaging business,” Youell said. “I was selling for another company and we decided to start our own company based in Columbus. We had six locations in five states and primarily supplied the auto industry, including Lear, Faurecia, Magna.”
They didn’t deal directly with the Detroit Three or other automakers.
Always suppliers.

P2Packaging owner Rudy Youell sits last month with a couple of versions of his P2 product box. They are custom built to fit dimensions of products and fold flat after use to allow them to be used up to 10 times. They are assembled at Anchor Bay Packaging in New Baltimore. Ryan Garza, Detroit Free Press
Youell jumped into the box business after graduating from Parkside High School in Jackson. At one point, while working in a factory running presses, he got his hands caught in a punch press and ended up in rehab for two years. His hands were crushed.
“Luckily, they didn’t get cut off,” Youell said. “I had to have bone surgery and skin grafts. I’m not a trust fund baby. Dad and I started our own business and then sold it.”
He added, “My father passed away this year. He never had a bad day in his life. When 2008 hit, I got the bankruptcy attorneys on speed dial and said, ‘Dad, we’re going down.’ He said, ‘Nah, don’t worry about it.’ He was a happy sales guy.”
Now, Youell is carrying on the family trade with his son.
“The product is so simple,” Youell said. “It’s like, ‘Duh.’ Not not like the cure for COVID. It’s just a frickin’ box. But in the automotive world, it’s a game changer.”
Patent details are available on the website www.2packaging.com.
Share This Story, Choose Your Platform!
Marx Layne is your competitive advantage.
Your reputation and success are our only concerns.